PLASTIC EXTRUSION TERMINOLOGY
Every industry has commonly used terms and acronyms, and custom plastic profile extruders are no exception. The extrusion industry tends to take these terms for granted, which can lead to confusion. Below are some of the common terms explained.
Extruders and Tooling
Think of extrusion in terms of an everyday product that almost everyone has seen – the extrusion of pasta using a pasta making machine. These devices make a wide variety of pasta noodle shapes, each using basic extrusion principles. In reality, whether you are making pasta or custom plastic profiles, the processes are very similar. Let’s look at 9 terms related to custom profile extrusion, all related to the extruder and the tool.
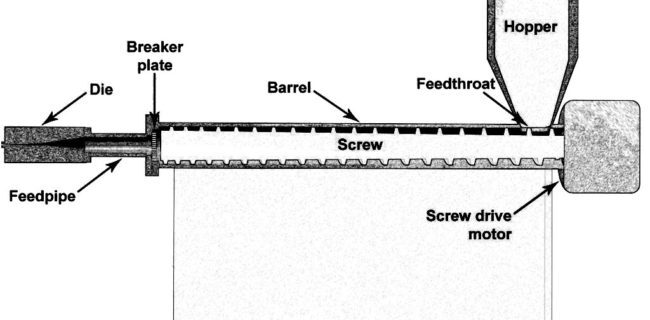
Extrusion Screw
Extrusion screws are the work-horse of the extruder. They convey, compress, and mix plastic compounds. Screw design for plastic extrusion is a sophisticated science, with specialty screw designs being developed to increase output rates, increase mixing, and widen processing windows. Screw designs may vary depending on the plastic compound, output requirements, and physical property requirements of the finished product.
Single-Screw Extruder
A single-screw extruder has one screw. It was the first type of extruder developed around 1935 in Hamburg, Germany. Single-screw extruders are widely used today for processing a wide variety of plastic compounds and are considered a work-horse extruder for custom profile extrusion.
Twin-Screw Extruder
Twin-screw extruders were developed in Italy after the Germans developed single-screw machines. Custom plastic extrusions are typically made on counter-rotating twin-screw machines while co-rotating twin-screw extruders are used primarily for compounding of plastic materials.
Counter-Rotating Extruder
Counter-rotating extruders are designed to have the screws turn toward one another (one turns clockwise, the other turns counter-clockwise), and the screws are intermeshed to mix and convey the material down the extruder. There are two different types of counter-rotating extruders.
A parallel twin-screw extruder has two parallel screws that are the same diameter from the beginning to the end of the screw.
Conical twin-screw extruders have a much larger screw diameter in the back of the machine, and the screws taper as material flows toward the die. Both types of twin-screw extruders provide a tremendous amount of mixing and compression of materials.
Extruder Size
Formtech has a variety of single-screw machines varying in size from ¾” to 3 ½”, which can accommodate profiles as small as 1/8” to over 8” in width. In general terms, the larger the diameter of the extruder, the more pounds per hour of output the machine provides. Twin-screw extruders are typically measured in millimeters, and can vary widely in size depending on the extruded plastic profiles being manufactured. Formtech has twin-screw machines from mid-range up to large sizes, which can handle profiles as small as under 1” and up to 12” wide profiles that weigh more than 7 pounds per foot.
Barrel
The barrel of the extruder is a hardened steel cylindrical cavity designed to house the extruder screw(s). The barrel is subjected to a considerable amount of pressure from compression of the plastic compounds during extrusion, and may either be simply hardened, or for high volume applications the barrel can be lined with harder materials such as tungsten carbide.
Hopper
Plastic compounds are fed to the extruder through a hopper, which is basically a funnel to hold material as it is being either gravity or force fed to the machine. Generally, as the size of the extruder and output increases, larger hoppers are required to act as a reservoir for the plastic compound. At Formtech, our primary extruders are equipped with vacuum loaders, allowing our operators to focus on the quality of the custom extrusion instead of spending valuable time manually filling the hoppers.
Adapter
Plastic materials exit the barrel and screw end, and are funneled into the extrusion die. The adapter allows the extrusion tooling to be mounted to the extruder, and transitions the material flow from the barrel & screw to a shape. The adapter can be a slide in configuration or can bolt on the head of the extruder. Slide in adapters provide ease of changeover from one extrusion die to the next, but are prone to leakage. Bolt on adapters take more time to change over, but provide a better opportunity for even pressure and reduced gate leakage. Many custom profile extruders utilize a series of standard adapters that can be used over a variety of extrusion tooling, to reduce tool costs and increase manufacturing flexibility.
Die
Think of the extrusion die as the gateway to your finished profile. The extrusion tool is what determines the shape of the finished profile. Typically, a custom profile die is made up of several die plates, and will transition the general shape from the adapter to the finished shape of the extruded profile. This is called streamlining, and it is critical to the extrusion process to control tolerances.
Have you ever made pasta and have certain strands not push out as quickly and evenly as others? This is due to improper streamlining, and the same holds true when manufacturing plastic extruded profiles. Many plastic materials are subject to degradation with heat, so smooth flow in the extrusion die is extremely important to eliminate burning during the production run. The streamlining in the die keeps plastic materials flowing, and helps prevent material degradation. The streamlined portion of the die feeds into the die land, which is the area of the extrusion tool where the material flows consistently across a section of the tool without streamlining. This land area stabilizes the material flow, and helps improve the surface finish of the extruded shape by “ironing” the outer surface of the profile.
The point where the plastic compound exits the extrusion die is referred to as the die lip. It is important to keep the die lip flat and sharp, and this requires careful handling by the extrusion manufacturer. If this lip is damaged, it can result in irregularities in surface finish and appearance. Formtech maintains extrusion tooling at both manufacturing facilities with proper inspection, handling, and care. Formtech manufactures many of the extrusion dies we use to manufacture custom plastic products. We also utilize a global network of world-class tooling vendors for additional extrusion tooling support.
Heater Bands
Precise temperature control is one of the processing musts in plastic extrusion. While the plastic material is in the barrel and screw of the extruder, a combination of friction heat and barrel heaters are used to carefully control the temperature of the extrudate. Once plastic compounds enter the adapter and die, external heaters are required to evenly control the compound temperature until the material exits the die lip. The die heaters can be as simple as strip heaters mounted to the extrusion die, or as sophisticated as custom made plates with flexible heater cords or even die inserts specially designed for the extrusion tool.
Downstream equipment
In this section, we are going to tackle the top 10 thermoplastic extrusion terms relating to ancillary or downstream equipment used to manufacture custom plastic profiles, tubing, and other hollow profiles.
Gravimetric Feeder
Above, we discussed that the hopper holds material that is fed into an extruder. These can be as simplistic as a steel “funnel” configuration that does little more than hold and feed material to very precise feeding systems that rely on gravimetric measurement to deliver accurate amounts of plastic material to the barrel and screw of the extruder. In tight tolerance situations, you will find many extrusion lines outfitted with this type of equipment.
In the case of a custom color matched, single durometer extruded profile, you would have a natural color base compound and a color concentrate. This can be done with a gravimetric feeding system that feeds two materials to the extruder at the same time. When appropriate, a three-station unit can be used to feed in precise amounts of reprocessed plastic to manufacture the finished extruded profile in the most environmentally friendly way.
Vacuum Calibration
Prior, we compared plastic extrusion to pasta making. Both processes use “ingredients” that are fed into an extruder, conveyed down the barrel with a screw, and are forced out a die to make a specific shape. In the case of pasta, there is very little heat created during this process. However, to make plastic into a product using the extrusion process, both frictional and external heat are used.
The heat forces the material through the extrusion die, then the manufacturer must capture the profile to maintain the overall shape and integrity of the profile during the cooling process. Water, other liquid coolants, or air can be used in the cooling process. Tolerance requirements may dictate that vacuum calibration (also called vacuum sizers) be built and used to capture the profile, using vacuum to hold the extruded profile in place during the cooling process. Most vacuum sizers today use water for heat removal.
Cooling Systems
Methods of cooling are dependent on the profile design. In some cases, a simple water-pan can be used to hold water or other coolant. This type of equipment is widely used in the extrusion of flexible profiles such as screen splines, extruded gaskets, and other smaller profiles. Another option is systems designed to hold guides and coolant.
However, to manufacture more complex products (window lineal profiles, office partition base raceways, entry door seals, etc) the extrusion manufacturer may use a calibration table. As the name implies, this is a very rigid stand that is designed to allow both vacuum sizing and water cooling tanks to be mounted for cooling and sizing purposes. The calibration stands vary in length to accommodate a wide variety of extruded plastic profiles. Typically, this type of stand has self-contained vacuum pumps along with both water and air supply with quick-change couplings to reduce set-up time during tooling changeovers.
Embossing or Texturing
Many extruded profiles you see have textured or embossed patterns on the exposed surface. The next time you are in a commercial building look at the extruded handrails and corner guards protecting the walls and corners in the building. Most of these products will have a pebble grain embossed pattern on the surface to add to the aesthetic appeal of the product, while offering the protection and durability high impact, rigid plastic materials provide.
Another great example of textured, or embossed products are the baseboards or wire raceway covers on open office partitions. These panels are subject to abuse from foot traffic as well as cleaning equipment, and the textured pattern helps minimize cuff marks and scratches. Formtech has embossing equipment at both manufacturing locations. Patterns can vary from a typical pebble grain, to custom designs, or to wood grain textures resembling real wood.
Tape Applicator
Many plastic extrusions have double-sided adhesive tapes, or even magnetic strips, applied to them for additional functionality. Some examples of this added functionality on extruded plastic profiles would include point of purchase display tags, Velcro®, automobile body side moldings, wall protection corner guards, and weather stripping. Anytime you hear the term 'peel and stick', this is the added functionality the addition of pressure sensitive adhesive tapes can provide to your extrusion.
Need to attach a vinyl extrusion to a piece of steel? Formtech can custom apply magnetic tape to the extrusion that will attach to a metal surface. You don’t need to attach to steel? Double-sided foam and non-foam adhesive tapes specially formulated to adhere to a wide variety of surfaces can be applied to the plastic extrusion on an in-line process to maximize function and minimize cost. Formtech has considerable experience with tape application, and we have specially designed tape applicators that can be used for many custom extruded shapes.
Haul-Off
In extrusion jargon, you will hear many terms used to describe a puller, conveyor, or haul-off, which is used to pull and convey extruded profiles down the extrusion line before being cut to lengths you can see from the picture below, top and bottom cleats, or belts, are used to apply pressure on the extruded profile as it is being pulled downstream. The belts can be made from a variety of materials, including foam, silicone or even rubber. Careful adjustment is required to maintain the plastic extruded profile integrity, without distorting the shape as the product passes through the unit. In many cases an additional speed controller is located near the extruder so the line operator can speed up or slow down the haul-off when controlling the size of the extruded profile.
Cut Off Saws
Plastic extruded profiles are linear products, and must be cut to length before they are removed from the extrusion line and packaged. A traveling saw is used primarily with medium to large profiles. The traveling saw, or progressive saw, clamps onto the profile to move the cut-off saw downstream with the product until the saw can cut through the extrusion. A progressive saw has the blade contained in the bottom of the unit, and it travels up through the plastic part. This can help control dust and saw chips more effectively when this type of saw can be used.
Fabrication Punch
The traveling saw has limitations, and is used only when extruded profiles are square cut at a 90° angle, or some consistent angle to make a trapezoid shape. This simplistic cut works for many customer applications where mill lengths are manufactured, or no additional fabrication is required. One of Formtech’s strengths is the capability to do additional inline and offline fabrication. Many of the extruded products Formtech manufactures are components in OEM products. We strive to provide the extruded profiles completely finished when possible, including more sophisticated end cuts, holes, punch-outs and other fabrication that allows less labor and handling at your plant.
Fly Knife Cutter
Have you ever wondered how drinking straws are manufactured? These tiny tubes are extruded, and extrusion lines to manufacture these products run at speeds that can manufacture over 180,000 straws per hour. The only way to cut a plastic extrusion at this type of rate is to use what it commonly called a fly knife cutter. As the name suggests, the unit has one or more knives on a rotating wheel that cuts through the plastic extrusion as the wheel rotates. Many of these units are servo driven, meaning the blade can be extended to cut, and then retract at very high speeds. The blade, or blades, can also be fixed in an extended position to provide one or multiple cuts per revolution of the flywheel on the cutter. Fly knife cutters are typically used for small to medium size extruded profiles and can include cutter guides for very clean end cuts on the end product.
Digital Length Gauge
Extrusion dimensions are often measured in thousands of an inch, and we provide our teams with equipment that can accurately measure to this level. The operation of a digital length gauge is fairly simple. The measurement device is mounted to a very accurate set of linear rails, and the part is inserted onto the unit for measurement. One end of the plastic extrusion is held up to a fixed stop, and the rail on the opposite end slides along the linear rails until it contacts the other end of the extruded profile. The actual length of the part being measured is displayed on a digital read-out, with measurements showing to three or more decimal places.
Materials
In this section, we are going to address material terms you may hear extrusion suppliers talk about when they discuss plastic materials. Extrusion companies tend to specialize in a group of raw materials. Formtech specializes in the following thermoplastic materials.
ABS (Acrylonitrile Butadiene styrene), Acrylic (Polymethyl Methacrylate), ASA (Acrylonitrile Styrene Acrylate), Butyrate (Cellulose Acetate Butyrate), WPC (Wood Plastic Composites), PC (Polycarbonate), HDPE (High Density Polyethylene), LDPE (Low Density Polyethylene), LLDPE (Linear Low-Density Polyethylene), MDPE (Medium Density Polyethylene), PP (Polypropylene), PS (Polystyrene), Rigid PVC (Polyvinyl Chloride in a hardened form), Flexible PVC (Polyvinyl Chloride with plasticizers), TPR (Thermoplastic Rubber)
Thermoplastic
Any material, such as Polyethylene, PVC and ABS, which can be re-melted and reprocessed without considerable loss of properties or scrap loss. In other words, the scrap materials, both post-industrial and post-consumer, can be recycled and reused into other useful products. This differs from thermoset materials, such as fiberglass, that set up permanently during the curing process. These thermoset materials cannot be ground and reprocessed. As a point of interest, Formtech is actually a net consumer of reprocessed materials, meaning we use more than what we make during the manufacturing process. With an eye on green manufacturing, we practice manufacturing techniques that reduce scrap, and we aggressively seek out products and industries that allow us to practice environmental stewardship.
Compounding
Resin is the classic definition of a plastic material prepared for subsequent manufacturing processes, specifically in extrusion and molding. Compounding is a process of blending plastics resins with other additives, and melting the materials during a heating or melting process. This process changes the physical, thermal, electrical or aesthetic characteristics of the plastic. Compounds can be tailored to a specific application, and by using a wide range of additives and fillers specific performance parameters can be met.
Dry Blend
A dry blend is a free-flowing blend of compound, or resin, and other ingredients as prepared for extrusion. Dry blend materials are important for processors that have twin-screw extrusion equipment available that can utilize the powder materials without the additional step of making pellets. Formtech has a variety of twin screw extrusion lines in our Athens, Georgia manufacturing facility that utilize dry blend compounds. By using the powder form, or dry-blend, the pelletizing process has been eliminated.
Color Concentrate
Not everything is black and white, and the plastics industry is a classic example of this. You will likely see red, or blue, or green, or yellow, or a rainbow of other colors in use in plastics around you. Formtech employs a wide variety of color concentrates to make a rainbow of colors depending on the application.
Pellets
Resins or mixtures of resins with compounding additives similar in shape or size that have been extruded or chopped into short segments to prepare them for molding operations.
Processing Aid
An additive or component in a compound to facilitate processing. Some raw resins, like PVC, cannot be extruded without processing aids and other ingredients that help bind the material together during the melting and extrusion process. Processing aids can also improve surface aesthetics of the finished part by allowing the material to flow through the tooling.
Composite
By definition, a composite is a material consisting of a combination of materials. Typically, one of the materials is a strengthening agent, the other being a thermoplastic resin or compound. Formtech manufactures a wide variety of composite products using wood fiber as the strengthening agent and PVC as the thermoplastic material. By utilizing these ingredients, we can increase stiffness and at the same time reduce thermal expansion and contraction. These physical properties are important in industries like construction, transportation, and a variety of other markets.
Processing
In this section, we are going to dive into processing terms you will likely hear a plastic extrusion supplier use when talking about the process.
Weld Line or Sink Marks
During the design of a plastic extruded profile, areas where intersection legs occur are prone to a visible line opposite where the legs intersect. First, what causes the line. If you take a close look at a drawing for a plastic profile with an intersection leg, you will see there is more mass in the area of the intersection. Since thermoplastic materials shrink some during the cooling process, the intersection of two legs cools at a slower rate than the rest of the profile, causing it to shrink more due to the mass of the profile.
As extrusion tooling is being designed, there are “tricks of the trade” used to minimize this line, or sink mark in the final part. A tool designer would typically separate the flow of the two legs within the die, and allow them to come back together as the extrudate is being compressed to the front of the extrusion die. This can in some cases create a weld line where the two melt streams are brought back together so careful tuning of the extrusion tooling is critical to minimize this line.
Another option is to turn the potential issue into a design feature, by designing indentations on the side opposite the intersection leg. The drawing below shows some options for designers to consider when dealing with a custom profile extrusion with intersecting legs to create features on the exposed surfaces.
Camber & Bow
As extruded profiles are being conveyed down the extrusion line, the cooling process begins. Common methods of cooling plastic extrusions include water, air, and even a combination of both depending on the product. In some cases during high speed extrusion, warm water may be used so the surface of the product is not shocked, which could cause physical property issues.
In the case of multi-hollow extruded plastic profiles, cryogenic cooling using nitrogen may be used to rapidly cool the inner legs of the extrude product to maintain profile integrity and increase line rates. Even, consistent cooling during the conveying period is critical to maintaining straightness of the extruded profile.
There are two terms used by plastic profile extrusion companies; bow and camber, to define lack of straightness. An extruded profile is considered to have bow when the part exhibits side to side warping. Camber is a term to define up and down warping of the profile. Generally, tolerances are set-up during the design and tooling development phases, and then checked as part of the ongoing quality assurance checks performed during production of the plastic profile extrusion.
Cross Section
The easiest way to define cross-section is to look at the end of the product in a two-dimensional view. The above illustrations (under weld line) demonstrate the cross section of the four examples showing ways to design around sink marks. In this case each of the four drawings show different cross sections of the extruded profiles. Cross sectional drawings of profiles are used by the Formtech quality assurance group and our production operators for quality assurance measurements and checks. The drawings are dimensioned, with tolerances to allow multiple quality operations to be performed using a variety of equipment such as digital calipers, micrometers and optical comparators.
Back Pressure
If you look the overall extrusion process, thermoplastic materials are under some type of compression from the time the material enters the hopper on the machine, until the material exits the front of the extrusion die. The compression area just before the extrusion die and flowing through the extrusion die is measured in pounds per square inch (PSI). Too little backpressure during this process will result in loss of profile integrity and physical properties. Too much backpressure can cause safety concerns as well as potential equipment damage, so it is important for the extrusion operator to monitor back pressure during the process using pressure gauges on the extruder and inserted into the die.
Tolerances
The custom plastic extrusion process involves melting plastic, forcing it out of the extrusion die, and then controlling the plastic profile shape and size at the part is cooled. As with any manufacturing process, the extruded profile will vary slightly during the process necessitating tolerances on key dimensions.
Tolerances on plastic extrusions impact fit and function, and the best time to start looking at tolerance requirements is during the initial design phase. By working with Formtech early in the process, we can provide design for manufacturing assistance including tolerance requirements. Typically, a control print will be developed by our quality assurance group to include dimensions and tolerances for critical dimensions, along with a control plan for use by our manufacturing and quality assurance groups.
Bulk Density
Bulk density is defined as the weight per unit volume of the plastics purchased by Formtech for use in custom extrusion applications. Bulk density impacts flow and feed rates on the extruder, and variations in bulk density of the plastic will cause variations in size so it is an important consideration for custom extrusion manufacturing operations.
Die Swell
We talked about back pressure above, and the importance of having the appropriate amount of back pressure during the extrusion process for physical property control. The back pressure is caused by compression inside the extruder and extrusion tooling. Once the plastic compound exits the extrusion die in a compressed form, the compound will relax, or expand slightly. This is referred to as die swell.
Die swell is material specific, meaning for example a vinyl (PVC) material will experience a different die swell than a Polyethylene or Polypropylene compound. Experience tells our tooling engineers the amount of die swell we typically get by material, and this is a critical consideration in tooling design.
Purging
In the extrusion process, cleaning materials out of barrels, screws and plastic extrusion tooling takes time and increases cost. For instance, if material changes are being made on the line from one job to the next, this could involve removing and cleaning the die, pulling the screw on the machine to clean, and brushing out the barrel of the machine while the screws are out.
Ultra-stabilized compounds have been developed that allow cleaning all these items, and flushing the system using these purging compounds. In fact, the purging materials are so stable they can even be left in the extrusion die during storage, put back on the extruder the next time the job needs to run, and started without time consuming cleaning. The normal compound will push the purge out of the die when it exits.
Another use for purge compounds would be during shutdown for weekends or holidays. Formtech extrusion technicians use purge materials when shutting some lines down for these periods to clean and protect the extruder and die. For some materials like Polyethylene and Polypropylene this is not required, but for PVC for instance, the material will degrade within the tool if it is left to cool and then be reheated for start-up.
Starve Feeding
When operating an extruder, materials are fed to the extrusion screws and barrel to make the plastic extrusion. There are really two methods that can be used to accomplish this feeding process.
First, the material can be contained in a hopper directly above the feed-throat of the extruder and fed by gravity. The screws will then take in the maximum amount of material they can with every revolution of the machine, and this is called flood feeding.
An alternative to flood feeding is to add a metering device at the feed-throat to control the amount of material introduced to the screws. The flights of the screw are not completely filled with every revolution of the screw. This is called starve feeding of the extruder, and offers some advantages to the extrusion technician in certain situations. By not filling the screw channel completely, it offers more control to the technician, and removes some other variables that can occur with flood feeding.
Surging
Surging is bad! Surging has always been one of the most common process variation on a single screw extruder. For every revolution of a single screw machine, there is some slippage back over the flights of the screw. This slippage is advantageous for mixing of materials and colorants, but it creates an opportunity for some surging and variation with the screw revolution.
With this being the case, differing pressures as material comes off the screw can cause this processing issue for the extrusion technician. Surging means variation, and this can impact size & tolerance control. Proper screw design for the type of plastic compound being extruded is extremely important to the process to minimize surging.